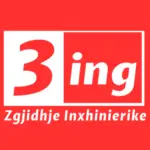
Testing and certification are critical components of ensuring that electrical installations, whether in residential, commercial, or industrial settings, comply with safety standards, regulatory requirements, and operational performance expectations. Proper testing and certification ensure the safety, reliability, and efficiency of electrical systems while minimizing the risks of electrical faults, hazards, and fire risks.
This process involves verifying that all electrical systems are installed correctly, safely, and function as designed. It also provides a means to identify and rectify potential issues before they lead to equipment damage, electrical shocks, or fires.
1. Key Aspects of Testing Electrical Systems
Electrical systems undergo a range of tests to ensure their functionality and compliance with safety standards. These tests typically fall into the categories of installation testing, functional testing, and periodic inspections.
a) Pre-Installation Testing
Before an electrical system is connected to the main power supply, various components must undergo pre-installation checks to ensure they meet design specifications and safety requirements.
- Insulation Resistance Testing: Ensures that the insulation of cables and conductors is free from faults, and that there are no unintended paths of current (such as short circuits).
- Continuity Testing: Checks for the correct continuity of conductors, especially in earth connections, to ensure there are no breaks in the wiring.
- Polarity Testing: Verifies that connections in outlets and switches are properly wired, ensuring that live (hot), neutral, and earth wires are correctly installed.
- Earth Fault Loop Impedance Testing: Ensures that the earth fault path is of low enough resistance to trip circuit breakers and protect users from electric shock.
- Visual Inspections: Before testing, a thorough visual inspection of wiring, components, and installations is conducted to check for any obvious physical issues like exposed wires, loose connections, or incorrect component placements.
b) Functional Testing
Once the system has been installed and connected to power, functional testing is performed to ensure that all components perform as expected under normal operating conditions.
- Load Testing: Ensures that the electrical system can handle the required load without overloading, causing damage, or tripping circuit breakers. This includes testing lighting circuits, power outlets, and appliances under typical or maximum usage.
- RCD (Residual Current Device) Testing: Verifies that the RCDs will trip as required in case of an earth fault or leakage of current to ground. This test simulates fault conditions and ensures the device operates within the specified time and current values.
- Circuit Breaker Testing: Ensures that circuit breakers trip at the correct current values (overload protection) and respond promptly to short circuits.
- Earth Leakage Testing: Measures any leakage of electrical current from the system to the ground. It is particularly important in older installations to ensure no risk of electric shock.
c) Functional Testing of Safety Systems
- Emergency Lighting Testing: Emergency lighting systems must be tested for function and duration to ensure they operate correctly in case of a power failure.
- Fire Alarm and Smoke Detector Testing: Verifies that these life-safety systems are wired and functioning as required, including proper response time and operation under various conditions.
- Uninterruptible Power Supply (UPS) Testing: Checks the performance of backup power systems that ensure continuous power supply during outages. The system must be tested for both the transfer time and the capacity to support critical systems.
d) Post-Installation Testing
After installation and initial testing, periodic testing ensures the system remains compliant and functional. These tests should be carried out at regular intervals, depending on the type of system, the environment, and usage.
- Thermal Imaging (Infrared Testing): Infrared cameras detect overheating in electrical components (such as switches, breakers, or cables). Overheating can indicate faulty connections or overloading, preventing serious problems like fires.
- Voltage and Current Testing: These tests check that voltages and current levels are within acceptable limits and that there are no voltage fluctuations that could damage equipment or cause inefficiency.
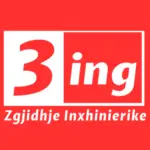
2. Standards and Regulations for Testing and Certification
Testing and certification must comply with national and international electrical safety standards and codes. These regulations ensure that electrical systems are safe, reliable, and efficient.
a) National Electrical Code (NEC) (USA)
- The NEC provides standards for the installation of electrical wiring and equipment in the U.S. It includes safety regulations for power distribution, circuit protection, grounding, and wiring methods.
- NEC includes provisions for testing and inspection of new installations, maintenance practices, and testing for safety and functionality.
b) IET Wiring Regulations (BS 7671) (UK)
- The BS 7671 standard (also known as IET Wiring Regulations) governs the design, installation, and testing of electrical systems in the UK.
- These regulations ensure compliance with safety standards, with specific requirements for testing before, during, and after installation to ensure that systems meet necessary performance standards.
c) International Electrotechnical Commission (IEC)
- The IEC sets international standards for electrical and electronic technologies, covering everything from product safety to system design and installation.
- IEC 60364 outlines the general rules for electrical installations, including testing and certification procedures.
d) Occupational Safety and Health Administration (OSHA)
- In many countries, compliance with OSHA regulations is required to ensure that electrical systems are installed and maintained in a way that protects workers from potential electrical hazards.
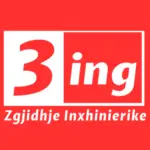
3. Testing Instruments and Equipment
Various instruments are used during electrical testing to assess the integrity and safety of electrical systems. Some of the key testing equipment includes:
a) Insulation Resistance Testers (Megger)
- Purpose: Measures the resistance of insulation in wiring and electrical equipment to ensure it is adequate to prevent leakage currents.
- Application: Used to check for insulation degradation, moisture, or physical damage.
b) Multimeters
- Purpose: A versatile tool used to measure voltage, current, and resistance.
- Application: Often used to check the operation of circuits, troubleshoot faults, and ensure proper voltage levels.
c) Earth Resistance Testers
- Purpose: Measures the resistance of the ground connection to ensure it provides a safe path for fault currents.
- Application: Checks if the ground rod and bonding system provide low resistance to earth for safety.
d) Circuit Tester (Voltage Tester)
- Purpose: Verifies the presence of voltage in circuits and ensures that electrical systems are de-energized before maintenance work.
- Application: Used to ensure that outlets, circuit breakers, and other components are safely de-energized during testing and maintenance.
e) RCD/RCBO Testers
- Purpose: Ensures that Residual Current Devices (RCDs) or Residual Current Breakers with Overload protection (RCBOs) trip at the correct current values in case of a fault.
- Application: Commonly used in testing safety devices and verifying that they operate within the prescribed limits.
f) Thermal Imaging Cameras
- Purpose: Used to detect hot spots in the electrical system, indicating possible problems such as poor connections, overheating, or equipment failures.
- Application: Useful for preventive maintenance and identifying hidden issues that may not be visible during visual inspections.
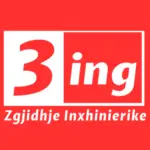
4. Certification Process
Once testing is complete, the system is often certified by a qualified professional or accredited testing body. This certification confirms that the electrical system complies with applicable codes, regulations, and safety standards.
a) Inspection and Report
- A detailed inspection report is produced, documenting the tests carried out, results, and any deficiencies or recommendations for improvement.
- The report should be signed off by a licensed or qualified electrician or electrical engineer.
b) Certification of Compliance
- Upon passing all tests, a Certificate of Compliance is issued. This certifies that the electrical installation meets all necessary safety and functional requirements.
- In some jurisdictions, a third-party inspector may need to verify and sign off on the electrical work to ensure it adheres to local regulations.
c) Ongoing Certification
- For periodic checks, systems may need to be re-certified after a specific time or after significant modifications or upgrades. Ongoing inspections ensure continued compliance with safety standards and operational efficiency.
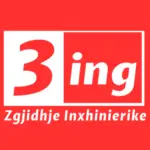
5. Conclusion
Testing and certification of electrical systems are vital to ensuring their safety, functionality, and compliance with regulations. Electrical systems that undergo thorough testing and receive proper certification are less prone to faults, hazards, and inefficiencies, providing a safe and reliable power supply to users. By using appropriate testing equipment, adhering to national and international standards, and conducting regular inspections, electrical installations can be maintained in optimal condition, reducing the risk of electrical accidents and improving overall system performance.
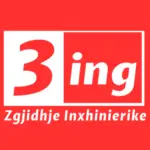